インタビュー
お客さまの世界一を目指して
- 3Dプリンターの新たな活用が自動車の性能を高める -
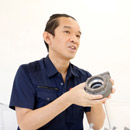
吉﨑 寛
2008年、SOLIZE 株式会社に入社。金型事業部にて試作金型の製造に従事。2016年からはSOLIZE Products株式会社(現SOLIZE株式会社)に移籍。開発部にて金属造形技術開発担当。学生時代の専攻は材料科学。専門知識を活かした開発を行っている。
近年、3Dプリンターの用途に変化が起きている。短納期を活かした試作品製作に加え、最終製品として実車に搭載される事例も出てきている。3Dプリンターの新たな使い方が、自動車の性能を高めるカギとなっている。SOLIZEでは、自動車の開発現場における課題の解決という視点から、3Dプリンターの性能を120%活かすための技術開発に取り組んでいる。最前線で開発を行っている開発部のエンジニアに、その舞台裏を聞いた。
― 開発部で取り組んでいる内容について教えてください。
開発部の仕事は、ニーズの調査から技術開発まで、多岐にわたります。ビジネス開発目線でお客さまのご要望に応じた具体的な提案ができるよう、お客さまとの打ち合わせに同席することも多く、研究に没頭している、というイメージとは異なります。ですので、テーマを探すところから行います。技術開発のテーマに関しては、大まかには造形条件レシピ開発、製品設計、後加工の3つに分けられます。そのうち、最近注力した開発テーマは、SUS316Lを用いた微細形状の造形技術と、SUS430の3Dプリンター適用で、両方ともレシピ開発に分類されます。
― 詳細を微細造形から教えてください。
厚さ0.2mmで空気が漏れない壁を作ることに成功しました。車載装置や、工場のラインの設備を冷却するための熱交換器に利用できるのではないかと想定しています。たとえば、ECUの冷却効率を向上させることは、電子制御技術の発展に寄与できるのではと考えています。ただ、3Dプリンターは複雑な形状の再現度が高いため、熱交換器以外にもさまざまな活用法が考えられます。
― 今まではできなかったのでしょうか。
標準的な造形条件では、厚さ0.5mmでも空気が漏れてしまうことがあります。熱伝達効率を高めるためには、可能な限り薄くすることが求められます。0.5mmから0.2mmで1/2以下の厚さになり、冷却効率が大幅にアップします。レーザーの出力や速度といった種々のパラメータを調整し、粉末材料の溶融の様子を観察しながら、最適な造形条件のレシピを作製しました。
― お客さまの反応はいかがでしょうか。
ありがたいことに多くのお問い合わせをいただいています。当初は垂直な壁しか作製できませんでしたが、ご要望に応えられるよう、さらにチューニングを重ねて曲がった壁も作製できるようにしました。これにより、入り組んだ形状も実現可能になりました。こういった要素技術が、お客さまの想像力を刺激する一助になればと願っています。
― 開発のテーマはどのように決めているのでしょうか。
技術トレンドの調査は行っていますが、お客さまの声がアイデアのヒントになることは多いですね。なので、無茶なご要望でも大歓迎です。SUS430に関しても、お客さまの声が開発のきっかけでした。
― なぜSUS430を3Dプリンター用材料として利用するのでしょうか。
エンジン開発、特にエキゾーストマニホールド等の排気系部品や、板金部品の試作に利用することを想定しています。
3Dプリンターで広く利用されているステンレスは17-4ph(SUS630同等材)という、日本ではあまりなじみのない材料です。量産時に使用する材料と異なる材料を試作で使用すると、評価しづらいので同じ材料を使いたい、というご要望は以前からいただいていました。そこで、排気系部品にはフェライト系ステンレスがよく利用されているため、その中で一般的なSUS430を選択し、造形条件のレシピを開発しました。3Dプリンターの強みの一つは短納期ですから、SUS430がお客さまの試験のリードタイム短縮に一役買ってくれるはずです。
ちなみに、私が調べた限りでは、海外を含めてサービスビューローでのSUS430の取り扱いは当社が世界初です。
― なぜ3Dプリンターの材料の種類は少ないのでしょうか。
使用できる材料の特性に条件がある(溶接割れしない等)ことと、造形条件のレシピ開発にノウハウが必要で、工数もかかるため、装置メーカー側もユーザー側も、気軽に試してみるにはハードルが高いのです。
― 新しい材料を使えるようにするのは難しいのですね。
そうなんです。使いたい材料を使えない、というのは大きな課題なので、それを解決するために、当社では特殊材料評価サービスを行っています。当社にはキャパシティとノウハウの両方がありますので。
当社の装置を使用して、お客さまの独自材料など、支給していただいた材料が造形可能か評価します。その後、支給材料を用いて当社内で生産を行う検討も可能です。過去にはタングステンや銅、フィラーを添加した材料、2種類の粉末を混合した材料など、さまざまな依頼をいただいています。
― 今後注力したい開発テーマは何でしょうか。
製品設計提案を含む、トータルでの3Dプリンター活用提案ですね。「どんな場面で3Dプリンターを活用するとメリットを享受できるのか」という、お客さまの問いに答えられることが、重要であると痛感しています。そのために、お客さまからお預かりしたデータに対するフィードバックだけでなく、お客さまの課題の解決方策を一緒に議論・検討したり、お客さまの現場をウォークスルーさせていただき、お客さまも気づいていない3Dプリンターの活用機会を見つけたりして、当社からも3Dプリンターの活用方法を提案しています。そして、3Dプリンターのメリットを最大限に活かした製品設計の際に重要となるトポロジー最適化や熱流体解析といった技術の活用や提案も進めていきたいと考えています。
後加工の開発に関しては、お客さまの保有設備によっても影響を受けるため、どこに狙いを絞るべきかを調査中です。
開発部の使命は、お客さまの課題を解決できる技術を開発することです。自分が世界一になるよりも、お客さまに世界一になっていただいた方が嬉しいですね。なので、独りよがりにならずに、お客さまの製品開発の背景を理解し、課題に寄り添った技術開発を目指します。
資料ダウンロード / お問い合わせ
サービスに関する情報をはじめとした各種資料(PDF)をご提供しています。
資料はまとめてダウンロードできます。お気軽にご利用ください。